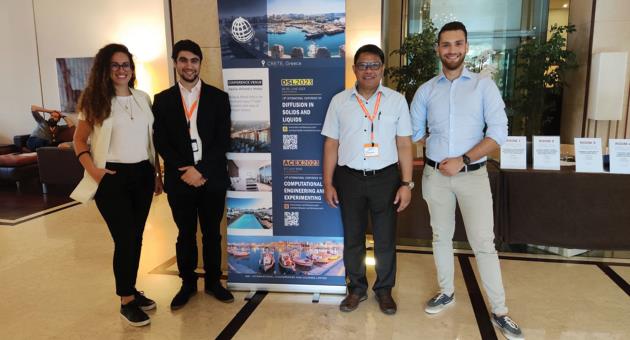
Three University students from the Department of Industrial and Manufacturing Engineering (DIME), supervised by Dr Arif Rochman, presented their studies in a special session on Additive Manufacturing at the ACEX2022 conference held in Florence from 4 to 7 July. This international conference, which was held for the 15th consecutive time, acts as a platform for delegates from academia and those in industry to share and develop their knowledge and communicate with one another on topics related to the Advanced Computational Engineering and Experimenting (ACEX).
Additive manufacturing, more commonly known as 3D printing, is a disruptive technology that has greatly advanced in these last few years. This process is able to build three dimensional (3D) objects layer-by-layer until the designed part is formed. The presented research focused on polymer-based 3D printing and these students, together with their supervisor, continued to contribute to knowledge in this exponentially growing research field.
The work presented by two of the students, Daniel Farrugia and Nadine Mifsud was carried out in close collaboration between DIME and Trelleborg Sealing Solutions (TSS) Malta. Daniel Farrugia had investigated on how to improve the interlayer adhesion of parts manufactured using polyether ether ketone (PEEK) and a filament 3D printer. Despite its high performance and heavy-duty applications, for example in automotive and medical sector, PEEK poses a challenge to be 3D printed, namely due to its low interlayer bonding strength. On the other hand, Mifsud presented her work titled Additive manufacturing and performance analysis of rubber components. Most of the published studies have analysed and evaluated the behaviour of components 3D printed from thermoplastics and there is little to no research on additive manufacturing of rubbers or thermoset elastomers. Hence, this study was very innovative and novel.
Albert Curmi demonstrated part of his work on Peek pellet 3D Printing, namely Thin Wall Peek 3D printing using direct pellet extrusion. His project focuses generally on developing a flexible 3D printing system to be able to 3D print parts from polymer pellets instead of filament, which could reduce the material cost up to around tenfold.
This project is supported by the Fusion R&I Technology Development programme of the Malta Council for Science and Technology (Project R&I 2018-009-T) and is led by the University of Malta and its industrial partner, Abertax Quality Limited.
Published in The Malta Independent on Sunday, 24 July 2022, 09:00